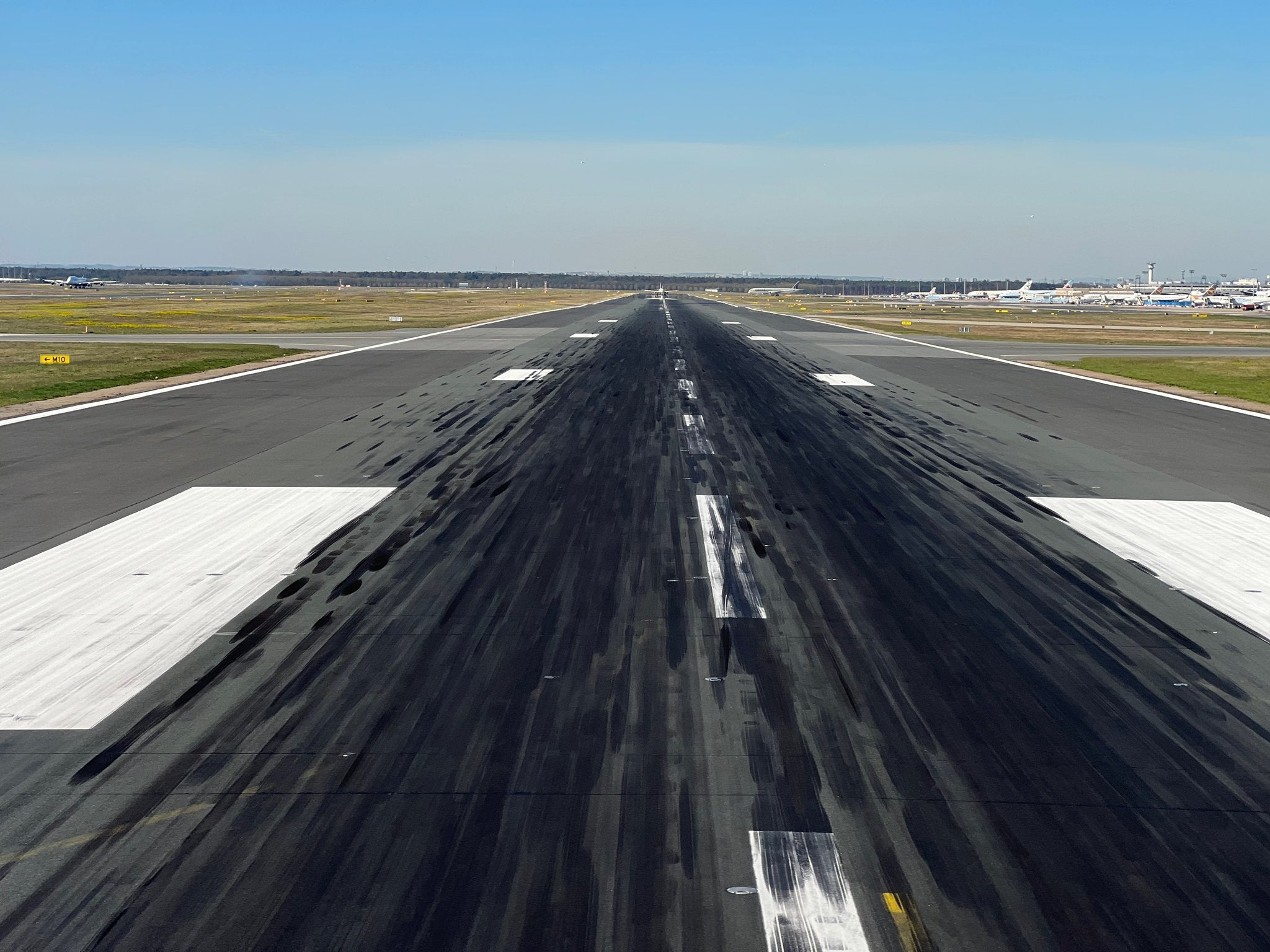
The maintenance of airport runways is crucial for passenger and crew safety, and removing hazardous rubber is a particular priority.
When a plane lands, each tyre leaves up to 1.5 lbs of rubber on the runway. When you consider an Airbus A380 has 22 tyres, the volume of the problem becomes clear.
A build-up of rubber on a runway makes the surface smooth, which is a huge issue. As a plane lands, the friction of the tyre hitting the concrete helps slow it down – the smoother the runway, the lower the friction.
Without that friction, it’s significantly more difficult to stop and control a plane – especially in wet conditions – and harder to see runway lines. It also creates an increased risk of foreign object debris (FOD).
How well do you really know your competitors?
Access the most comprehensive Company Profiles on the market, powered by GlobalData. Save hours of research. Gain competitive edge.

Thank you!
Your download email will arrive shortly
Not ready to buy yet? Download a free sample
We are confident about the unique quality of our Company Profiles. However, we want you to make the most beneficial decision for your business, so we offer a free sample that you can download by submitting the below form
By GlobalDataJet away: removing the rubber
“Every time a plane lands on a runway, up to 14kg of rubber can be deposited – especially in the touchdown zone,” says Alex Groom, business development manager at Jetting Systems, a UK-based firm that manufactures high-pressure water jet cleaning machines for rubber removal.
“This is usually a more significant issue in hotter, more humid climates, where deposits are greater because of the runway and ambient temperature, and there can be a greater risk of heavy rainfall. Larger, heavier planes will tend to leave greater deposits, as well as shorter runways where heavier braking is required.”
Groom explains that large international airports clean their runways three to five times per week. Each session takes up to four hours and typically takes place at night when the runway is closed.
Regional or less busy airports may undertake rubber removal at scheduled periods throughout the year. Hub-type airports that rely on connecting flights 24 hours a day have less time, so can utilise runway shutdowns or scheduled maintenance periods.
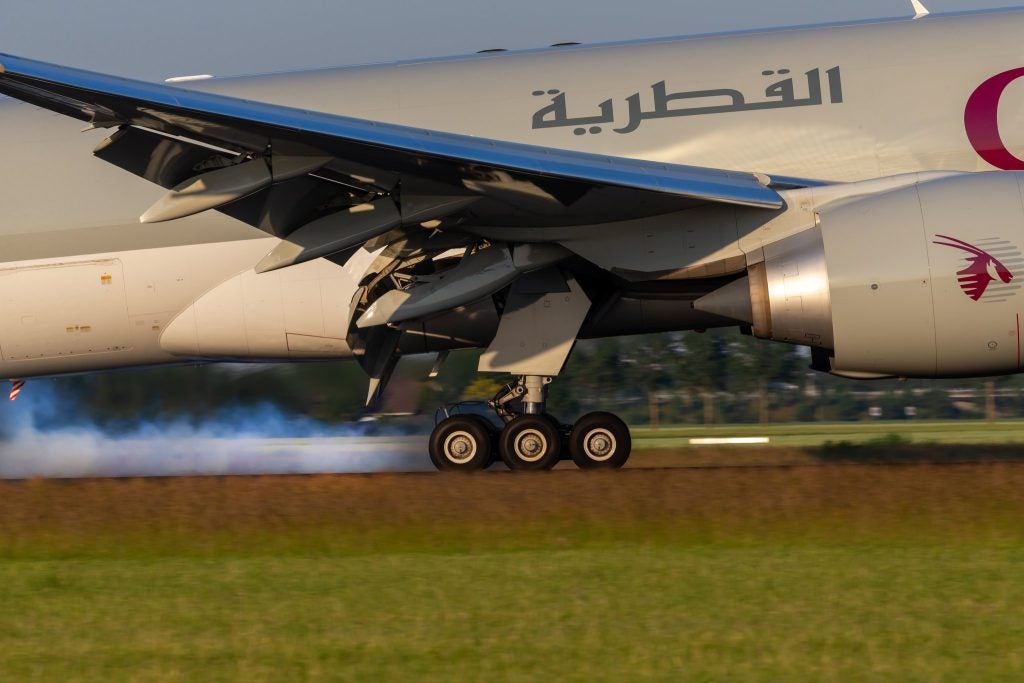
One of the more common ways to remove runway rubber is to use ultra-high-pressure water jetting. This approach uses rapidly spinning jets of water at a pressure of 2500-3000 bar. For comparison, a standard consumer-level high-pressure driveway cleaner would be about 100 bar, and mains water in the UK is about four bar.
Groom says that Jetting Systems’ Osprey system jets the rubber off the runway pavement, and then recovers the wastewater and debris. It means the runway is ready to use as soon as the truck leaves the runway and as waste is collected, the wastewater and debris can be disposed of according to local regulations.
“Water jetting is fast, effective, and non-polluting. When used correctly it does not pose a risk of damage to the runway surface,” he says.
A robotically controlled lateral system, Groom explains, can completely remove all rubber deposits without damaging the runway, whilst a linear system will remove deposits slightly faster but less thoroughly. The unique lateral system follows grooves in the pavement, while the linear traverses it.
Runway cleaning is all about timing
There are alternative methods to remove rubber from runways, including chemicals and scrubbing. As a majority of the chemicals used for rubber removal need special handling and aren’t environmentally friendly, airports tend to prefer to use other methods for removal.
Groom believes these other methods are generally expensive, less effective and have a high possibility of polluting the environment too. They also require a runway to be closed for longer periods of time. Removal rates are relatively lower as well – perhaps 35-45%.
“Our equipment can get on and off the runway in under a minute. Our larger equipment can remove up to 6,000 square metres of rubber an hour, so even short access of 30-40 minutes can make a difference if done regularly,” explains Groom.
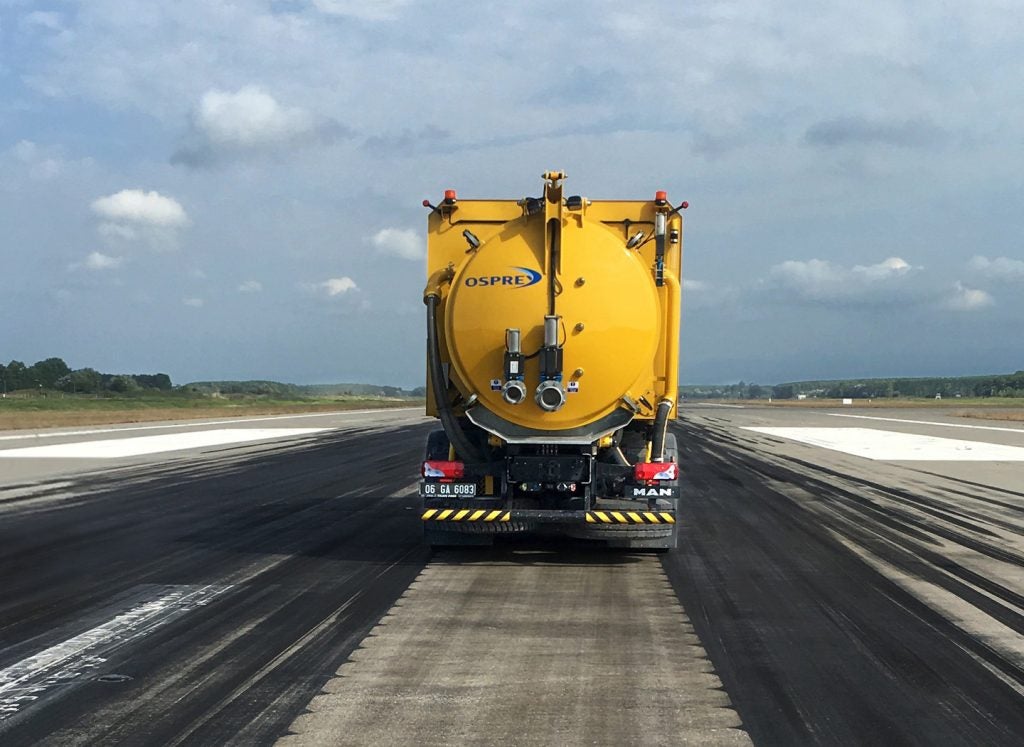
Jetting Systems provides its equipment to airports around the world, including hubs in the UK, Turkey, Kuwait, Vietnam and Namibia.
The equipment is expected to have a 15-year lifespan or even more, and the company works closely with owners to ensure the appropriate training and maintenance plans are followed.
“We are innovation-led so rely on a close relationship to understand how equipment can be adjusted or modified to improve effectiveness, productivity, safety or sustainability,” adds Groom.